Using Fusion 360 to Design and then Print a Box Insert for Better Organization
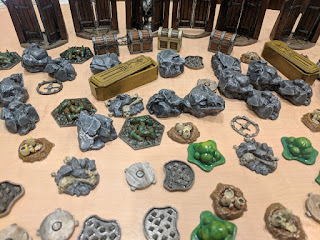
After picking up a few storage boxes, I went about sorting my pieces. I decided to put them into a fairly large box that had removable dividers along the rows, which worked out pretty well... except that I ended up using almost every cell in the box. I had to remove a bunch of dividers for the doors and the boulders and the cave stone pillars (which aren't even in that picture!), but the cells were too big for many of the other objects (such as the various traps, the nests, the pressure plates, and even the treasure chests).
Because I'm a huge nerd, when I saw that, I thought to myself, "if I subdivide these cells along the vertical axis, I can multiply my storage capacity!" If I was a normal human being, I'd probably just think, "I could fit a few layers of stuff in this box!" but that phrasing only occured to me later.
The first step in this process was to measure everything. Since this box had removable dividers, there were little nubs that protruded into the rows (to keep the dividers in place), so I had to measure the distance between the inside of those nubs, the depth of them, as well as the height of the cells, the distance between the sets of guide nubs, and the total length that I wanted to use for my subdivided sections. I decided that I wanted my subdivision to be 3 cells wide (so would interface with 2 pairs of guide nubs), but I wanted it to fit inside a pair of the standard dividers (so that the cells to either side of my insert wouldn't be compromised if/when I lift my insert out).
I pulled out my calipers and captured all of those measurements, grabbing them at multiple points along each length (so that I'd know my shortest, or worst case scenario, distances). When measuring the width of my rows, I failed to measure at the bottom though, which caused me a bit of trouble later (it was really hard to get the calipers down to the bottom of that channel).

Next, I drew a pair of long thing rectangles, starting slightly above my box and ending slightly below the bottom. These would eventually become the interfaces for the nubs (and the dividers that would replace the ones that the box came with for this section). When drawing these rectangles, the exact sizes and placement didn't really matter, as dimensioning the pieces would straighten that out for me later.

Once I was here, I decided that it was time to print a prototype, so I extruded the outer-most perimeter and divider walls by 1 mm, exported the STL and printed it. I slid it into my case and noticed a problem - while it fit great at the top of the row, it squeezed and got caught mid-way down when I tried to push it to the bottom. The guides for the dividers were apparently tapered slightly, so were wider at the base. Fortunately, this was easy to fix in Fusion 360; I literally changed that one dimension measurement down to 62 mm and was good to go.
At this point, I figured that the box was basically ready to extrude and then print. So, I modified my previous test extrusion, ensuring that I had selected the outer wall, the divider walls and the nubs, then extruded them upwards 25.5 mm. I then selected the 3 floor sections and extruded them upwards by 1 mm, ensuring that the Join option was selected on the extrude.
Once that was done, I had a nice box, which I exported as an STL and then sliced. That's when I looked at my printer spool and saw this. Slic3r reported that this model was going to take something like 14 meters of filament to print. I didn't know how much filament was on there, but I didn't think that I had 14 meters, so it was time to get creative. If necessity is the mother of invention and laziness is the father, I suppose stinginess must be an uncle or something? This family tree is getting confusing. Well, I wanted to reduce the amount of filament that I was going to use, both because I was almost out and because there is generally no reason to use more plastic than necessary.
Since the walls and floor were already so thin, the best way to remove material seemed to me to make cutouts. Instead of boxes, I needed baskets. I figured that roughly 2 mm wide bars (with similarly sized gaps) would be a good design, since my terrain pieces were generally larger than that. I knew that I wanted a solid border around the edges of each panel for strength (so, no gaps at the edges), so I drew in a guide line (draw a normal line, then select it and press X) on the floor of my cell and dimensioned it to be 2 mm away from their respective edges.



Since the walls were a solid extrusion upwards, I couldn't draw the slats into the initial sketch. Instead, I decided to make them in new sketches, one from the front and one from the side, which I could then extrude out and cut the holes in the extruded walls. To make this more easily printable, I decided that I'd use vertical bars on the walls (instead of horizontal), which might leave me with a bit of stringing to clean up but would only require bridging at the very top of the slats (and even then, only across the roughly 2 mm gaps, which is nothing to worry about).


When all was said and done, I exported my new shape as an STL and Slic3r came back with a 7 meter estimate. It's still a lot of plastic when you're used to working with miniatures and props for miniatures, but it was a lot better than the original design! So, I printed out 2 of them, and they fit perfectly, one on top of the other, in the row of my storage box.
If anyone wants a look at my files, I've uploaded my subdivider basket files. That said, if you're at all interested in learning to model, I recommend making them yourself, as they aren't that complex but offer a really good chance to learn how to use CAD.
Comments
Post a Comment