Making Meshmixer Supports
I've written tidbits of this information across a few other support-related posts, but I figured that I should put it all in one place. I've been printing a lot of minis lately, which has meant that I've had to learn a lot about supports and 3D printing. I use a Prusa MK3, so this post is focused on FDM supports. I tried a lot of different support structures across several different programs and my favorite ones were tree supports in Meshmixer. I know many others have had excellent results with other supports, but I've been happy with my results and so that's what I'm going to write about :P
Generating tree supports via Meshmixer is a 2 phase process. First, you've got to figure out your print's orientation, and second, you've got to figure out your actual supports. For minis, that first step can be a difficult balancing act, as you probably don't want supports to connect to the most detailed parts of the mini (like its face). You also have to keep in mind your nozzle width - any surface that's parallel to your printer bed is going to have a resolution limited by that nozzle width.
What that means is that, if I lay a model down completely on its back so that its nose is pointing straight upwards, that nose had better be at least as wide as my nozzle, otherwise it literally cannot print. If the model is standing upright, on the other hand, the nose will jut out the side of the face and part of that nozzle width can actually be buried inside the head.
Besides considering the print quality of my model, its orientation also affects its stability on the printer bed. If I want to print a sword, for example, I could lay it down flat or I could balance it on its tip. One of those two would almost certainly fall over during the print and fail.
On the other side of that same coin though, is the number of supports required. A sword that's balanced upright on its tip probably only requires 1 support, as the whole thing will build upwards from that supported tip (that's assuming it doesn't burn down, fall over and sink into the swamp). If you lay it flat on the printer bed, it's probably going to need a whole bunch of support, due to the way the blade tapers towards the edges. Even with those supports, you're probably going to get a pretty bad print on the underside. So, where's the happy medium? In this case, right in between the two extremes.
FDM printers can generally print at 45 degree angles without too much trouble. So, angle that sword 45 degrees upwards and add a few supports. You'll definitely need supports at any low points (say, the pommel and the low side of the cross-guard), but you may need a few others for stability. Throughout this whole printing process, this thing is going to be shaken back and forth with every Y axis movement. While all that shaking is going on, it's going to be pressed down upon by the nozzle as it extrudes new layers. Occasionally, it might even experience some abrupt lateral forces, if the print nozzle collides with it due to warping during the cooling process.
When I'm printing something at a steep angle, I make sure it's got a lot of support, especially at the bottom. I like to put additional supports where I can on the way up, just to give the object some stability to hopefully resist those otherwise destructive forces that it will be subjected to. This holds true for both the object that I'm printing and for support structures themselves.
Meshmixer has a tool to help you explore different object orientations that may print better. If you go to Analysis -> Orientation, you'll get 3 options: Strength, Support Volume, and Support Area. Basically, these are the priorities that Meshmixer is going to weigh when determining which orientation it'll suggest.
Strength is all about minimizing the number of thin (weak) spots on the print. I don't care much for this one, personally, as minis don't experience *that* much stress during printing. Support Volume tries to make the overall print smaller, so that it uses less filament. I'm as cheap as the next guy, but PLA isn't that expensive, so I don't care too much about that one either. Support Area tries to minimize the area of the model that is going to need supports. That one is pure gold. Fewer supports means less work during cleanup and less chance that I'm going to break something important while prying off some stubborn bit of support material. I usually start with 10 under Support Area, and 0 on the other two, then tweak them from there to try and see some other options. In this case, my usual "Support Area Heavy" values actually ended up with him upright, so I messed with the values to get a funny angle for the screenshot :P
I love looking at the suggested orientations, but I don't take them as gospel. For example, minimizing the overall support area might mean leaving some crucial bit completely unsupportable. But, looking at Meshmixer's suggestions can help me to think more clearly about my model and often serves as a good starting point. That said, I frequently end up printing the model completely upright with extra supports, because that will often leave the most visible surfaces looking best.
To make those supports, I go to Analysis -> Overhangs to open up the supports window. I've settled on these as good settings for me, so they may serve as a good starting point for anyone working with these supports:
Angle Thresh: 45
Contact Tol: 0
Y-Offset: 0 or 3 mm, depending
Max Angle: 45
Density: 10
Layer Height: <the height that I am going to print my mini at, typically 0.05 mm)
Post Diamter: 2.5 mm
Tip Diameter: <my nozzle diameter, so .25 mm)
Base Diameter: 6 mm
Allow Top Connections: Unchecked
Optimization 0
Solid Min Offset: 0.02
Tip Height 1 mm
Base Height: 0.4 mm
Strut Density: 0
Post Sides: 7
Right away, I'm faced with a decision: do I want part of this model to print directly on the printer bed, or do I want the whole thing to "float" on support trees? If my model has nice big feet with lots of contact area, I'll usually print it with those feet on the bed. That guarantees that they're perfectly flat, which will make them easier to glue onto a base later (and require less support over all, which means a faster print).
If the feet aren't so big (like on the City Archer model), that style of printing can have a problem - feet can come detached from the printer bed. Maybe it's time for me to do an acetone wash on my bed (rather than the standard IPA washes that I do before every print), but I've had a couple of those models lose a foot during the print. It prints the leg part way up, then at some point the foot comes loose and shifts (but doesn't go far because it's entangled in support material). I've been fortunate that there was only a little spaghetti before the thigh resumed printing (on top of the spaghetti), so a little bit of glue and putty actually made the prints usable. That said, it's still a situation best avoided. That's when I use the Y Offset.
The Y Offset raises the whole model by N mm (Meshmixer's Y axis is Blender's Z axis). When I want to "float" a mini, I usually set it to 3 mm, which is plenty of room for the tree to build but isn't too terribly wasteful. When floating the City Archer, I ended up putting something like 8 support trees on the bottom of each foot. I wanted to make sure that they printed flat and I really didn't care if they had some markings from support removal. That also gave the legs a very strong connection to the supports, which is important when they need to bear the weight of the entire model during much of the printing process.
After I've decided if I want to use a Y Offset, I let Meshmixer generate supports. Then, I look at them to make sure that they make sense. During this step of the process, I'm looking for a few things:
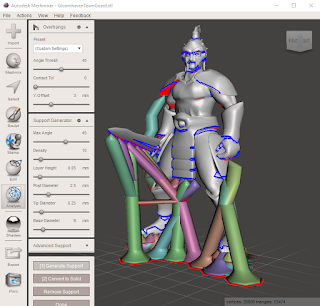
What that means is that, if I lay a model down completely on its back so that its nose is pointing straight upwards, that nose had better be at least as wide as my nozzle, otherwise it literally cannot print. If the model is standing upright, on the other hand, the nose will jut out the side of the face and part of that nozzle width can actually be buried inside the head.
Besides considering the print quality of my model, its orientation also affects its stability on the printer bed. If I want to print a sword, for example, I could lay it down flat or I could balance it on its tip. One of those two would almost certainly fall over during the print and fail.
On the other side of that same coin though, is the number of supports required. A sword that's balanced upright on its tip probably only requires 1 support, as the whole thing will build upwards from that supported tip (that's assuming it doesn't burn down, fall over and sink into the swamp). If you lay it flat on the printer bed, it's probably going to need a whole bunch of support, due to the way the blade tapers towards the edges. Even with those supports, you're probably going to get a pretty bad print on the underside. So, where's the happy medium? In this case, right in between the two extremes.
FDM printers can generally print at 45 degree angles without too much trouble. So, angle that sword 45 degrees upwards and add a few supports. You'll definitely need supports at any low points (say, the pommel and the low side of the cross-guard), but you may need a few others for stability. Throughout this whole printing process, this thing is going to be shaken back and forth with every Y axis movement. While all that shaking is going on, it's going to be pressed down upon by the nozzle as it extrudes new layers. Occasionally, it might even experience some abrupt lateral forces, if the print nozzle collides with it due to warping during the cooling process.
When I'm printing something at a steep angle, I make sure it's got a lot of support, especially at the bottom. I like to put additional supports where I can on the way up, just to give the object some stability to hopefully resist those otherwise destructive forces that it will be subjected to. This holds true for both the object that I'm printing and for support structures themselves.
Meshmixer has a tool to help you explore different object orientations that may print better. If you go to Analysis -> Orientation, you'll get 3 options: Strength, Support Volume, and Support Area. Basically, these are the priorities that Meshmixer is going to weigh when determining which orientation it'll suggest.

I love looking at the suggested orientations, but I don't take them as gospel. For example, minimizing the overall support area might mean leaving some crucial bit completely unsupportable. But, looking at Meshmixer's suggestions can help me to think more clearly about my model and often serves as a good starting point. That said, I frequently end up printing the model completely upright with extra supports, because that will often leave the most visible surfaces looking best.
To make those supports, I go to Analysis -> Overhangs to open up the supports window. I've settled on these as good settings for me, so they may serve as a good starting point for anyone working with these supports:
Angle Thresh: 45
Contact Tol: 0
Y-Offset: 0 or 3 mm, depending
Max Angle: 45
Density: 10
Layer Height: <the height that I am going to print my mini at, typically 0.05 mm)
Post Diamter: 2.5 mm
Tip Diameter: <my nozzle diameter, so .25 mm)
Base Diameter: 6 mm
Allow Top Connections: Unchecked
Optimization 0
Solid Min Offset: 0.02
Tip Height 1 mm
Base Height: 0.4 mm
Strut Density: 0
Post Sides: 7
Right away, I'm faced with a decision: do I want part of this model to print directly on the printer bed, or do I want the whole thing to "float" on support trees? If my model has nice big feet with lots of contact area, I'll usually print it with those feet on the bed. That guarantees that they're perfectly flat, which will make them easier to glue onto a base later (and require less support over all, which means a faster print).
If the feet aren't so big (like on the City Archer model), that style of printing can have a problem - feet can come detached from the printer bed. Maybe it's time for me to do an acetone wash on my bed (rather than the standard IPA washes that I do before every print), but I've had a couple of those models lose a foot during the print. It prints the leg part way up, then at some point the foot comes loose and shifts (but doesn't go far because it's entangled in support material). I've been fortunate that there was only a little spaghetti before the thigh resumed printing (on top of the spaghetti), so a little bit of glue and putty actually made the prints usable. That said, it's still a situation best avoided. That's when I use the Y Offset.
The Y Offset raises the whole model by N mm (Meshmixer's Y axis is Blender's Z axis). When I want to "float" a mini, I usually set it to 3 mm, which is plenty of room for the tree to build but isn't too terribly wasteful. When floating the City Archer, I ended up putting something like 8 support trees on the bottom of each foot. I wanted to make sure that they printed flat and I really didn't care if they had some markings from support removal. That also gave the legs a very strong connection to the supports, which is important when they need to bear the weight of the entire model during much of the printing process.
After I've decided if I want to use a Y Offset, I let Meshmixer generate supports. Then, I look at them to make sure that they make sense. During this step of the process, I'm looking for a few things:
- Is this model even printable? That is to say, are all of the low points connected directly to the printer bed by either supports or some other part of the model?
- If I have a low point (maybe a horn or something) that has no material under it, I have three options: draw more support trees, reorient my model, or cut a section off of the model so that it can be printed separately. That is my order of preference, as cutting bits off will either leave a seam or require putty during the cleanup phase, neither of which I like.
- How much weight am I expecting individual supports to bear? Is there a single support tree going up to a foot or something, which in turn will have to support a whole leg before that part of the model finally joins with another part?
- If I have a bunch of model that grows off of a single support, I just make more supports. I'll cluster a whole bunch of supports at that low spot, then add supports intermittently moving up the model (where I can). Ideally, I try to put a support tree every ~7 mm, which makes for a rock solid print. You can get away with a lot less than that, and you won't be able to manage it everywhere, but I like to do it where I can so that that part of the model will help to hold the rest in place during the print.
- If I have a single support tree that fans out to a bunch of support contact points, I try to reinforce that support tree just before the fan out occurs. That usually comes in the form of supports for the support, or as a bridge to another support tree. I just want to make that point more stable so that it doesn't move around while undergoing the stress from the material being printed onto it.
- Do I have supports that are connecting to sharp edges? In my Strong Support Trees article, I wrote about the way the slicer will abstract away fine points and edges, which might leave a gap between something like a sword tip and the top of the support tree.
- If my model needs support at places like this, I add extra support trees a little further up the weapon, where they can join to a flatter spot. I'll also try to position them sideways a bit, onto the flat of the sword rather than a thin edge. At this point, it's a balancing act between having enough supports that it'll print well, while not making it too difficult to remove the supports.
- Do I have supports that might warp upwards during the print? I'm looking for long supports that are around that magic 45 degree angle. While that might be printable, having a several cm long, 2.5 mm round bar shooting up at an angle from a single 6 mm diameter footprint is still pretty dicey.
- This another situation where I make supports for my supports. I draw bracing supports under my main support, getting them as close to straight up and down as I can (vertical supports seem less likely to warp than angled ones). I also draw bridges to other support trees sometimes - anything to help make the support less likely to move around during the printing process.
- Do a have a large enough footprint to prevent the print from coming detached during the print? I imagine what the first layer of the print is going to look like, since that's ultimately how much adhesion this print is going to have to the print bed. If my entire model is resting on just a few support trees' bases, that's a good setup for failure.
- When there's a very small footprint on the printer bed, I will sometimes draw short support trees that land next to my existing ones (so that they overlap a bit), just to enlarge their footprint. I'll also use that technique to "merge" two support trees, so that they'll have a single large first layer instead of individual small ones.
- If I'm floating my model on supports, I'll usually just generate a brim in Slic3r. That way, all of the support trees will be connected by a giant first layer, which in turn provides excellent bed adhesion. I've done this a few times while not floating my mini (mostly because I forgot to turn the brim off in my print options), and it worked fine... except that it added a fair amount of work to the cleanup process as I had to cut away that brim without damaging my model.
So, how's all of this look in practice? Well, take a look at my City Guard remix model. Like the City Archers, this guy has relatively small feet, so I'm going to use the Y Offset to float him entirely on supports. With that decided, let's look at the supports that Meshmixer has automatically created and go down the list.
Here's the supports that Meshmixer automatically generated. It's actually a bit unusual that it generated such a thick pile of supports under each foot - usually, the feet would be undersupported and I'd be left to draw in extras. In this case, I felt like there was too much support and was worried about the interfaces overlapping and making it difficult to remove. So, I ctrl-clicked every other support under each foot to delete it.
Next, I panned around the model and imagined how it would print. That single support going to the sword blade worried me. It went at such a steep angle that I was worried about it not printing well, so I drew another support bar nearly straight down to the ground, then added a bunch of additional contact points to the edge of the sword. Supports in a row like that tend to be fairly easy to remove, as you can wiggle the support tree perpendicular to its flat axis and weaken them all at once (once it's been loosened from other supports). To add some stability, I drew a bridge between the sword supports and the supports between his feet.
Speaking of the stuff between his feet, I was worried about the bottom of that armor sagging during printing, so I added a few more supports to it. At that point, I took a look at his footprint and decided that I wanted a bit more material to be on the printer bed, to ensure that everything stuck well (since I'd had those foot-loose moments on earlier attempts). To do that, I just drew a few more diagonal supports so that all of their bases would overlap together.
Next, I looked at the other twisty support trees and added some bracing to them, to ensure that they wouldn't get out of place during the print. And, this is what I ended up with:
It printed really well! I accidentally snapped a foot off while removing some support on the first one (which was really odd, because the support came off of the foot itself without any difficulty), but superglue resolved that one nicely, and prints 2-4 didn't have any issues at all!
One really nice thing about this style of supports (especially in combination with a small nozzle): they actually remove really well. I've recently been focusing more on snipping the trees apart at the bottom, which often allows me to just pull them off of the model in whole pieces! In fact, check this out:
I got the whole support tree off of one of them in a single piece! That was more work than snipping them apart at the bottom, but I decided to see if I could manage it on one of these guys, since their support networks aren't overly complicated. I just found myself mainly using my cranberry knife to remove the supports via prying motions, since I couldn't get my wire cutters in there to snip at the interfaces with all of the other support in the way.
9/24/18 Update: Ok, there ended up being a Part 2 to this post after all...
Next, I panned around the model and imagined how it would print. That single support going to the sword blade worried me. It went at such a steep angle that I was worried about it not printing well, so I drew another support bar nearly straight down to the ground, then added a bunch of additional contact points to the edge of the sword. Supports in a row like that tend to be fairly easy to remove, as you can wiggle the support tree perpendicular to its flat axis and weaken them all at once (once it's been loosened from other supports). To add some stability, I drew a bridge between the sword supports and the supports between his feet.
Speaking of the stuff between his feet, I was worried about the bottom of that armor sagging during printing, so I added a few more supports to it. At that point, I took a look at his footprint and decided that I wanted a bit more material to be on the printer bed, to ensure that everything stuck well (since I'd had those foot-loose moments on earlier attempts). To do that, I just drew a few more diagonal supports so that all of their bases would overlap together.
Next, I looked at the other twisty support trees and added some bracing to them, to ensure that they wouldn't get out of place during the print. And, this is what I ended up with:
It printed really well! I accidentally snapped a foot off while removing some support on the first one (which was really odd, because the support came off of the foot itself without any difficulty), but superglue resolved that one nicely, and prints 2-4 didn't have any issues at all!
One really nice thing about this style of supports (especially in combination with a small nozzle): they actually remove really well. I've recently been focusing more on snipping the trees apart at the bottom, which often allows me to just pull them off of the model in whole pieces! In fact, check this out:
I got the whole support tree off of one of them in a single piece! That was more work than snipping them apart at the bottom, but I decided to see if I could manage it on one of these guys, since their support networks aren't overly complicated. I just found myself mainly using my cranberry knife to remove the supports via prying motions, since I couldn't get my wire cutters in there to snip at the interfaces with all of the other support in the way.
9/24/18 Update: Ok, there ended up being a Part 2 to this post after all...
So your settings are for a 0.25mm nozzle. Would you recommend changing any of the settings other than Tip Diameter for a 0.4mm one? Larger strut diameter as well for instance?
ReplyDeleteThe only thing that I'd change is the Tip Diameter (in fact, I started using most of these settings back when I was using a 0.4 mm nozzle). I think that a 0.4 mm nozzle could print a post as thin as 1 or 1.5 mm, but posts that thin snap too easily and tend to warp if they're longer than a centimeter. 2.5 mm posts seems to be the sweet spot, as far as balancing "snake-ability" and strength. After generating a basic support structure with 2.5 mm posts, you can start drawing short thinner posts (I usually use 1.5 mm) to connect to the stronger post network so that you can get into tight places without having long thin posts.
DeleteThis series has been really helpful as I try and use MM's trees instead of the builtin ones of S3D (which are hard has hell to remove properly.) Now I just can't seem to master getting the tips of things to launch right. If I have three tips near each other in varying heights one gets left off and that causes despooling. I need some test model to figure out these supports. Love the break away potential but getting them right is an artform.
ReplyDelete